As industries rapidly shift towards digitalization, the field of measurement and instrumentation has emerged as both a constant and a catalyst, anchored in precision while pushing innovation. As associate chief engineer at Technip Energies, one of the world’s leading EPC companies, Priyanka Kaul has a front-row seat to these transformations. In this exclusive interview with Instrumetrics World, Ms. Kaul reflects on the ever-evolving role of instrumentation, its impact on future operations, and the human skills needed to lead innovation into the future.
By Madeline McNabb & Christian Borrmann
With 22 years of experience in the energy sector, Priyanka Kaul has consistently been at the helm of large-scale international and Indian EPC
(engineering, procurement, and construction) projects with companies such as Fluor, KBR, L&T Hydrocarbon Engineering, L&T Technology Services, Desein, S&B Engineers and Constructors, and GS E&C. In her current role at Technip Energies, Ms. Kaul oversees instrumentation engineering activities for some of India’s largest industrial projects. She describes her work as both deeply technical and inherently collaborative; it requires not only a thorough understanding of the latest instrumentation technologies, but also a strategic mindset to ensure seamless integration of control systems across multidisciplinary teams.
Driving progress through landmark projects
At Technip, Ms. Kaul has taken on some of the most ambitious and technically complex projects in India’s energy and petrochemical sectors, showcasing her engineering expertise and underscoring the importance of instrumentation in enabling large-scale industrial transformation. Among her most notable contributions is her work on India’s first standalone refinery and the country’s first greenfield integrated refinery complex to be commissioned since 2016, representing a critical step in India’s journey towards energy self-sufficiency. “The refinery’s launch comes at a crucial time,” notes Ms. Kaul, “with India projected to surpass China in oil demand growth.”
Ms. Kaul also recently oversaw two other industrial-scale projects in India. The first, a PVC (polyvinyl chloride) plant, addressed a longstanding need to reduce the country’s dependence on imported PVC, a material widely used in construction, automotive, and packaging industries. The second project was a refinery off-gas cracker (ROGC). With an ethylene production capacity of 1.7 million MMtpa, it stands as the world’s largest ROGC facility to date. The scale of the project was matched only by the complexity of the instrumentation systems required to monitor and control its operations. According to Ms. Kaul, “as process industries continue to evolve, the role of instrumentation and control systems will remain at the forefront of innovation and progress.”
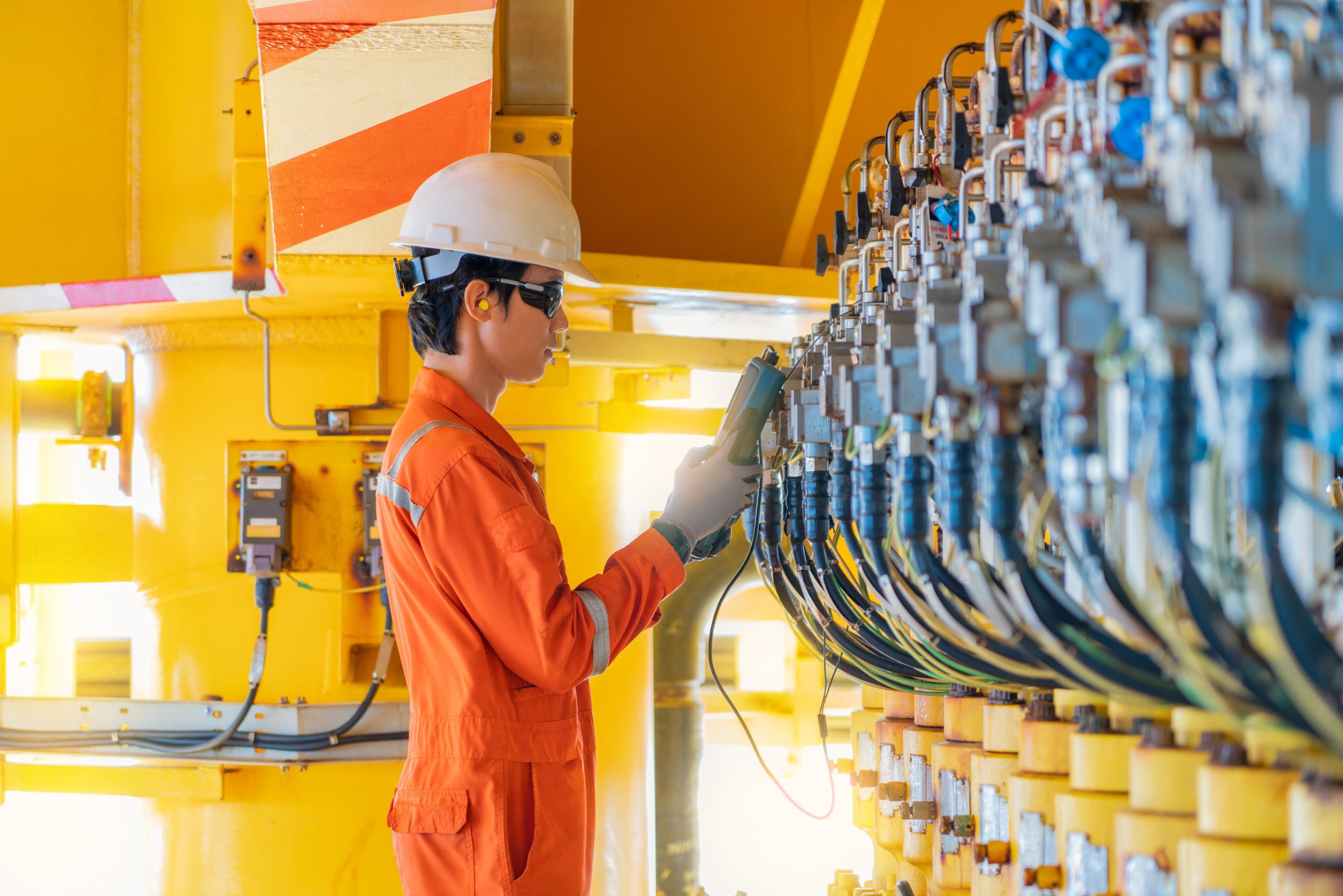
Integral to every stage of industrial operations
Control and instrumentation engineers play a pivotal role in optimizing industrial processes and ensuring the smooth operation of complex systems. From initial design and construction to commissioning, operation, and maintenance, instrumentation and control engineers are vital to a plant’s development.
Designing and implementing control systems to optimize process efficiency is one of the main responsibilities of a control and instrumentation engineer. “Control and instrumentation engineers analyze the existing processes, identifying areas for improvement, and developing strategies to enhance productivity,” explains Ms. Kaul. Using their understanding of both the existing processes and the technology available, the engineers select the most appropriate hardware and software components for each application to ensure seamless integration.
Once the design phase is complete, engineers oversee installation and commissioning, carefully calibrating instruments that monitor variables such as temperature, pressure, flow, and level. Despite careful planning and implementation, issues can arise in control systems over time. Engineers employ diagnostic tools and data analysis techniques to identify the source of any malfunctions or inefficiencies and fix those issues in the control system. Using advanced data analysis techniques and condition monitoring tools, engineers can predict potential equipment failures before they occur—reducing downtime, lowering repair costs, and extending the lifespan of critical equipment.
The backbone of industrial operations
Instrumentation ensures that systems operate within predefined parameters while prioritizing safety, optimizing efficiency, and adhering to
environmental standards and regulations. From controlling process variables to protecting workers and the environment, instrumentation is the backbone of industrial operations.
Safety is a cornerstone of instrumentation, helping prevent hazardous situations that could threaten workers, equipment, or the environment. Safety systems such as emergency shutdown systems, fire and gas detection systems, and safety interlocks are integral to industrial operations. “These systems automatically intervene in case of abnormal conditions to prevent accidents and minimize risks. They allow for quick shutdowns or equipment isolation when necessary, mitigating risks, preventing accidents, and safeguarding the well-being of all involved,” says Ms. Kaul.
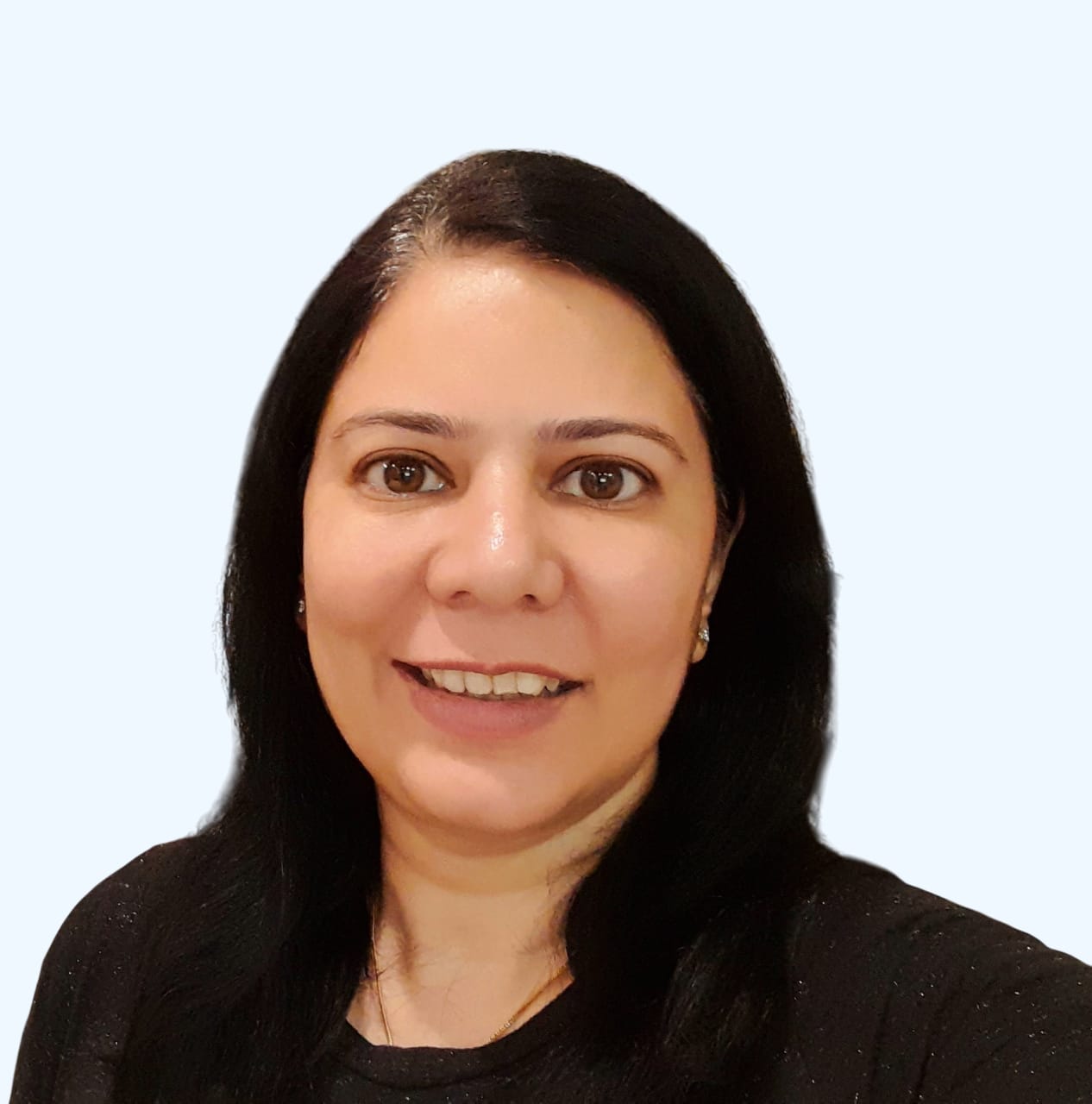
Sophisticated control systems streamline industrial operations. Control systems detect issues promptly and take corrective actions without delay, resulting in more efficient operations and reduced downtime. This capability is vital for maintaining product quality and increasing productivity, ultimately leading to higher output with less waste.
As environmental concerns grow, instrumentation has become essential in helping businesses meet environmental standards and regulations. “Environmental monitoring involves measuring ecological factors such as air and water quality, radiation levels, and pollutants through advanced instrumentation,” elaborates Ms. Kaul. The data collected can prompt immediate alerts, enabling industries to take corrective actions before they violate regulations. “Adopting accurate and reliable instrumentation reduces energy use and decreases environmental impact,” Ms. Kaul adds, highlighting how effective instrumentation can also contribute to sustainability goals.
Navigating complexity: Challenges in instrumentation engineering
While instrumentation engineering is central to modern industrial success, it is not without its challenges. From environmental extremes to evolving technologies and legacy systems, engineers in this field must constantly adapt, innovate, and collaborate. Each EPC project demands a custom approach, shaped by variables like site conditions, regulatory standards, and legacy infrastructure.
One fundamental challenge lies in selecting the right instrument for specific environmental conditions. Harsh environments like marine or cold climates often require rugged instruments and protective enclosures, making collaboration between process and instrumentation engineers essential.
Compatibility is also a recurring theme throughout instrumentation work. “Field instruments need to seamlessly integrate with the control system for data acquisition and process control,” explains Ms. Kaul. In revamp or expansion projects, compatibility can be especially challenging. “It is essential to carefully review existing plant documentation, including inventory lists and as-built drawings,” she says. Often, the existing systems are outdated, poorly documented, or even based on obsolete technologies.
Ms. Kaul recalls one such project with a previous company: a fast-track international workshare involving the revamp/expansion of an old refinery complex. The existing infrastructure was so dated that many documents consisted of scanned, handwritten notes. Ensuring compatibility between old and new systems required extraordinary coordination. “We overcame the challenges through excellent communication and collaboration across time zones,” she shares. “We held frequent meetings with the client, conducted adequacy checks to close any gaps, and had an on-site engineer who gathered firsthand information to guide the design and selection process.”
Cybersecurity is another growing concern in modern instrumentation and control systems, requiring secure communications, access controls, and active monitoring for vulnerabilities. Through expertise, planning, and teamwork, engineers like Priyanka Kaul are making today’s systems robust and ready for the future.
A smarter, greener future for instrumentation
The field of instrumentation is rapidly evolving, with new technologies like software-defined automation, industrial internet of things (IIoT), artificial intelligence (AI), and digital twin transforming industrial processes by enhancing automation, enabling remote operations, and improving safety and productivity. “These digital transformation trends aim to work alongside humans to do everything from improving communication to limiting repetitive work,” Ms. Kaul elucidates.
Wireless sensors and IIoT devices are central to this transformation, providing visibility into operations and enabling quick, data-driven decisions. “Wireless sensors measure and transmit the information either to the edge equipment or directly to the sensor cloud using various protocols like ISA100, LoRa, and Sigfox,” explains Ms. Kaul. Edge computing enables real-time data processing at the plant level, while cloud computing centralizes data for analytics.
By analyzing sensor data, AI can predict equipment failures before they happen. Digital twin also enables predictive maintenance and process optimization, further enhanced by AI to adapt to real-world scenarios. “By creating a virtual replica connected to the physical asset, digital twins give manufacturers the insights they need to make production decisions quickly,” Ms. Kaul says.
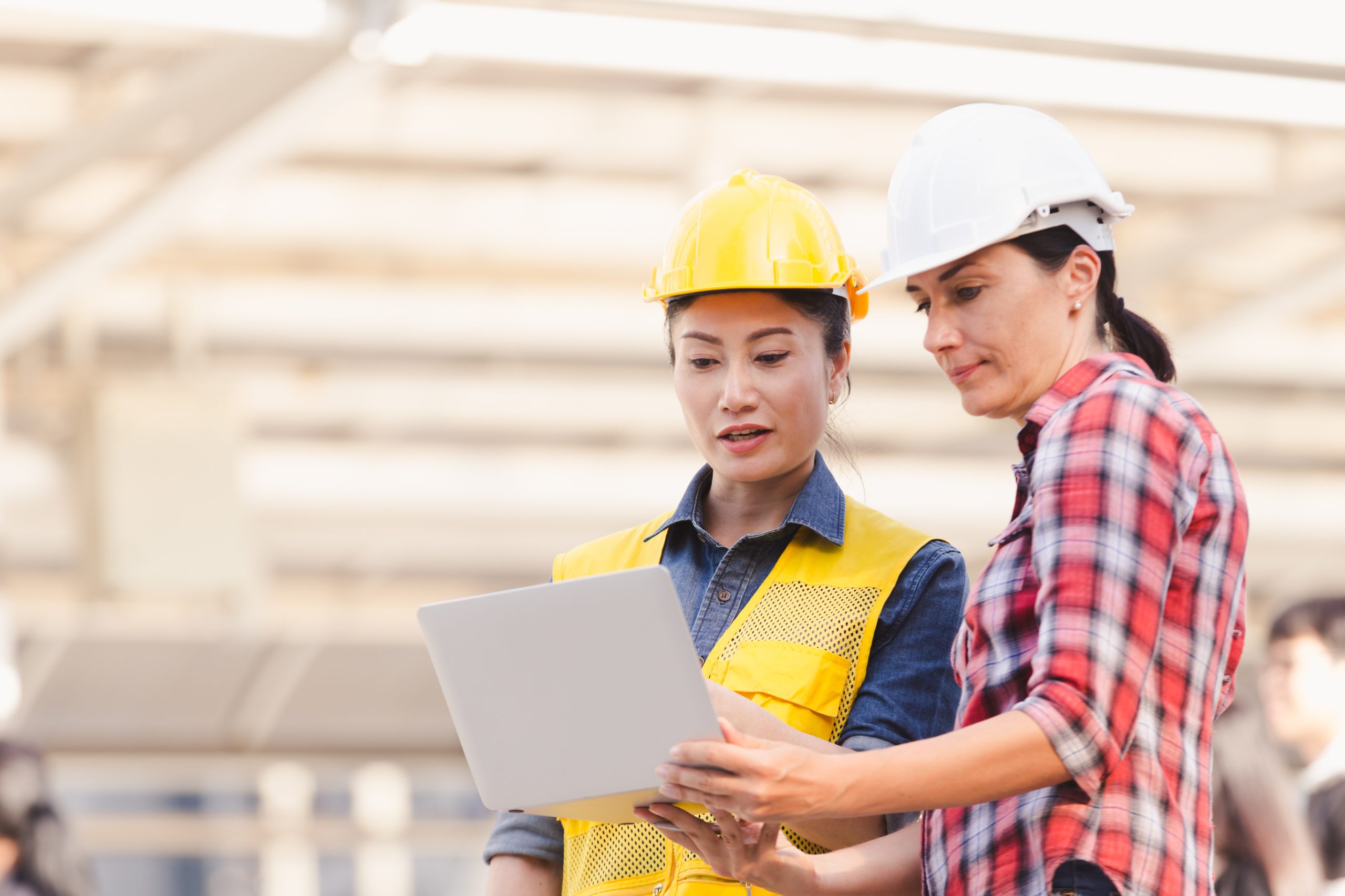
As industries worldwide continue to embrace Industry 4.0, the field of measurement and instrumentation is set to become more intelligent, interconnected, and indispensable than ever before. This technological shift is ushering in a new era of environmental accountability. “Digital transformation brings with it the power to collect, analyze, and interpret vast amounts of data,” says Ms. Kaul. “Process industries are now equipped to monitor energy consumption, carbon emissions, and resource usage in real time.” With data-driven insights, plant operators can make smarter decisions, adjusting operations to reduce waste, cutting energy costs, and implementing greener practices.
Together, these innovations point towards a future in which “instrumentation and control engineering make industries more efficient, proactive, and responsive to the needs of both the market and the environment,” Ms. Kaul concludes.
Advice to future engineers
For aspiring engineers looking to make a meaningful impact, instrumentation and control engineering presents a world of opportunity. “This field significantly enhances industrial operations’ efficiency and safety and provides numerous opportunities for innovation and professional growth,” says Ms. Kaul. As industries continue to adopt smart technologies and sustainable practices, the demand for skilled engineers is only set to rise.
Ms. Kaul also celebrates the progress being made towards greater inclusion in the engineering world: “It is a welcome change and inspiring to see many more women in leadership and engineering positions than 15 years back, due to diversity and inclusion initiatives that are being implemented in companies for empowering women employees.”
Instrumentation and control engineering is not just a career path; it is an exciting, challenging, and fulfilling journey into the heart of industry innovation.
Disclaimer: The views expressed are the subject’s own and do not reflect the opinions or positions of the subject’s employer.
“We regularly share Featured Stories with our Instrumetrics World community. Join us and let’s share your Featured Story on Instrumetrics World online and in print.”