Air Liquide has inaugurated a pilot site for the production of carbon-free hydrogen in Denmark.
After 42 years with Air Liquide, Hugo Willekens* has probably heard, seen, and done all there is to do in the field of instrumentation. Still, when we met up with the current North-Europe and CIS country (NEC) Cluster Expert for Instrumentation at Air Liquide’s office in Antwerp, Belgium, it was clear he remains totally focused on his work and is always keen to soak up knowledge and information about emerging technologies.
By David Sear
If like this editor you thought that industrial gases were produced at a central plant and distributed to customers in cylinders or by tanker truck, then you are partly right. Partly, because this is how some gases are indeed delivered to small and medium sized customers. But as Air Liquide’s Mr. Willekens immediately makes clear to us, larger customers are typically served in a very different way.
“What we have in the North-West of Europe, for example, is a network comprising dozens of local production plants. These facilities are typically located close to, or even inside, customers’ premises. This enables us to ensure the reliable provision of gases such as nitrogen, oxygen, hydrogen and carbon monoxide as required in sectors such as chemicals, refining and metals. Moreover, we have a wide network of pipelines to ensure these gases are as readily available as humanly possible.”
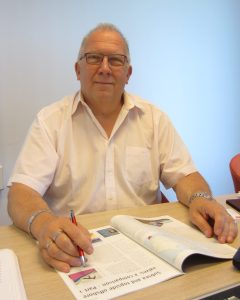
Mr Hugo Willekens, North-Europe and CIS country (NEC) Cluster Expert for Instrumentation at Air Liquide in Belgium.
Instrumentation and maintenance
‘Availability’ is in fact a recurring topic throughout our pleasant interview and one which is of course closely related to maintenance. Comments Mr. Willekens: “maintenance is an essential activity that is being actively considered by Air Liquide and indeed many other companies in a wide range of sectors. In the past, maintenance was predominantly done on a corrective level. Later we transitioned to a system of preventive maintenance, which involved extracting say a third of all instrumentation valves during a scheduled shutdown.
These would be cleaned, inspected, and repaired where necessary before being re-installed. However, there was a growing realization that this approach was not cost-effective, as sometimes half of the valves taken out were still in perfect working order. So our strategy now is to move to predictive maintenance. At this stage we are exploring various options for predictive maintenance as many control valve manufacturers – and certainly major suppliers such as Emerson, Metso, Samson etc. – have products available for this.”
Given Air Liquide’s focus on reliability, it will come as no surprise to learn that Mr. Willekens and his colleagues have thoroughly reviewed all the systems that are available and are currently running tests prior to making any final decisions. Mr. Willekens: “At this time we are evaluating the performance of a system which has been installed at one of our plants. Even if this is successful we will still keep our options open as we typically prefer having a number of approved sources for any product or service to ensure healthy competition.”
Traffic Lights
Developing the topic of maintenance, Mr. Willekens indicates that Air Liquide is also very interested in condition monitoring. “A couple of months ago we installed a software package at a plant in Antwerp that can give us feedback about the condition of the valve itself. Currently we are waiting for sufficient data to analyze to see how well this system work, but there are already
plans to introduce condition monitoring in a plant in Rotterdam soon. Our preference is to select systems that are genuinely smart. By this I mean that we don’t just want to receive data, but that the data should be automatically interpreted such that local operators can immediately see the status of a valve and have an indication of what action might be required and on what timeframe.”
Mr. Willekens further indicates that a straightforward visual system using traffic lights – red for immediate action needed, yellow for intervention advised but still safe to operate and green for working normally – would be very beneficial. “Just to give a simple example: suppose the gland packing is leaking then obviously the valve will need repairing at some stage but an immediate response is probably not essential. That can be conveyed by a yellow light. Building in security and reliability of this kind is certainly good for us and most definitely for our customers as well. I see such systems as part and parcel of the general transition to big data and the internet of things. The more information we can have, the better off we will be.”
The importance of testing
During the course of his forty-two year career Mr. Willekens has, of course, seen a great many changes in how instrumentation systems are operated. He remembers starting out with pneumatic devices based on a 0.2 to 1.0 bar system which was followed by electrical signals according to a 10 to 15 milliamp protocol followed by 4 to 20 milliamps. Later advances saw the
introduction of HART followed by fieldbus systems. And coming right up to date, he
was recently involved in the decision to introduce an ultra-modern digital positioner on absorber units. Mr. Willekens: “these units generate high purity hydrogen whereby certain valves are cycled every two minutes. Moreover, the time from opening to closing has to be two seconds or under. We therefore carefully analyzed a number of positioners and selected the one which best meets our needs. It was of course first tested extensively at the manufacturer’s facility and also in one of our units before being validated for use.”
Although digital technology and smart systems can bring benefits, Mr. Willekens recommends that end users such as Air Liquide should always thoroughly evaluate and test devices before actual installation. Interestingly, Mr. Willekens notes that, in addition to the network of plants connected
by pipelines, Air Liquide has another ace up its sleeve to ensure reliability of supply to customers. “As I have said, if a plant should be offline for whatever reason then essentially we don’t want customers to even know about it. That’s why we also store nitrogen and oxygen in liquid form. These liquids can be quickly re-gasified if needed to maintain pipeline pressure. But of course we try and make our processes as reliable as possible, for example by building in redundant systems in key areas. Which is why we fit double solenoids on valves that have an emergency shutdown application.”
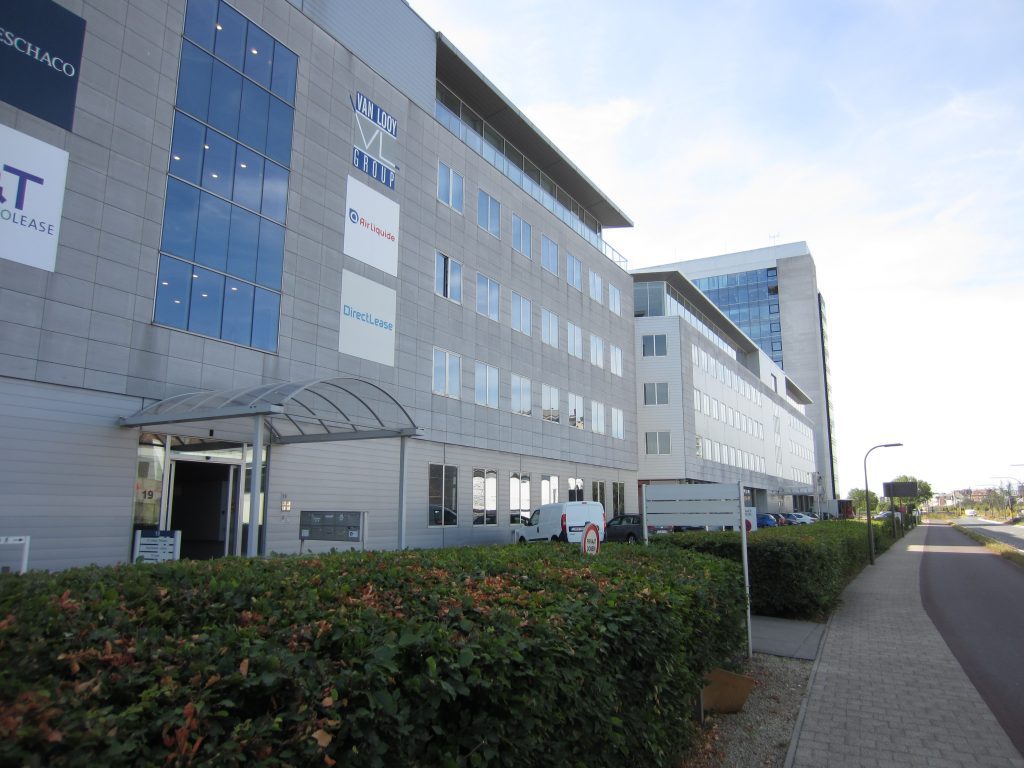
Meeting up with Mr Willekens at the offices of Air Liquide in Antwerp, Belgium.
Sharing Knowledge
As all instrumentation engineers will agree, common issues that require attention include control valve cavitation and inappropriate specification. Such concerns are certainly not unknown to Mr. Willekens. However, he also shared a couple of issues that are typical for companies such as Air Liquide and which he is currently monitoring. “In cryogenic systems such as the ones we have you can experience water vapor condensation in the bellows of bellowssealed valves. If that condensation then freezes, ice can form around the stem and could ultimately render the valve inoperable. We have this issue with a specific control valve brand and are working closely with the supplier to find a solution. Another concern that can be experienced with valves that are exposed to the elements is rainwater ingress into stem packings.”
All such incidents are thoroughly investigated, with the findings being widely shared with other instrumentation experts, instrumentation engineers and plant operators throughout Air Liquide’s operations. In addition, Mr. Willekens regularly writes documents presenting information on how to specify and maintain valves that are particularly geared to the needs of staff working within individual plants. “I do not wish to dictate rules but rather to share knowledge so that local staff can get the best possible performance out of their assets. Moreover, these guidelines can be of great value if plants are looking to undertake minor upgrades or extensions themselves. If they know more about why certain valves were initially selected, they will be better placed to make consistent selection decisions in the future.”
Sharing in-house
In addition to sending out written documents, Mr. Willekens has also started to organize annual ‘face-to-face’ events for colleagues working at the plant level within the field of instrumentation in the Benelux. Here he gives presentations on case histories, discusses future trends and highlights developments in supply to ensure that operators and technicians are as knowledgeable as possible about the control valves and other devices they are required to operate and maintain.
“Make no mistake about it, the field of instrumentation is tremendously dynamic,” he says by way of conclusion at the end of our interview. “An engineer starting out today in this field is in for a treat as he will be learning something new every day for the rest of his or her life. When I graduated no-one had heard of cyber security for example but this is a topic that will increasingly make the headlines. Oh yes, instrumentation is without doubt a fascinating and very rewarding discipline to work in!”
Meet Mr. Willekens
Joining Air Liquide in 1977 Hugo Willekens has always worked in instrumentation. From a junior position he has enjoyed increasing levels of responsibility, becoming the technical lead, the regional expert and then the Benelux expert for instrumentation. He is now the Northwest Europe cluster lead for instrumentation. Mr. Willekens is leader of Air Liquide’s European ‘Community of Practice’ for instrumentation. Attending the worldwide instrumentation CoP, as a member, gives him ready access to the knowledge and experience of a worldwide network of colleagues. Thanks to his citizenship and work Mr. Willekens is fluent in English, French, Dutch and German. Mr. Willekens is married with a daughter and two grandchildren, and sees green technology as the solution to many current issues.
About this Featured Story
*Mr Hugo Willekens is now in well-deserved retirement.
This Featured Story is an article from the archive of our sister publication Valve World Magazine, March 2020 issue. To read other featured stories and many more articles, subscribe to our print magazine. Available in both print and digital formats. DIGITAL MAGAZINE SUBSCRIPTIONS ARE FREE.
“We regularly sharea new Featured Storyies with our Instrumetrics World community. Join us and let’s share your Featured Story on Instrumetrics World online and in print.”